Caso práctico: aplicación del control estadístico de procesos multivariante (MSPC)
29 oct 2024
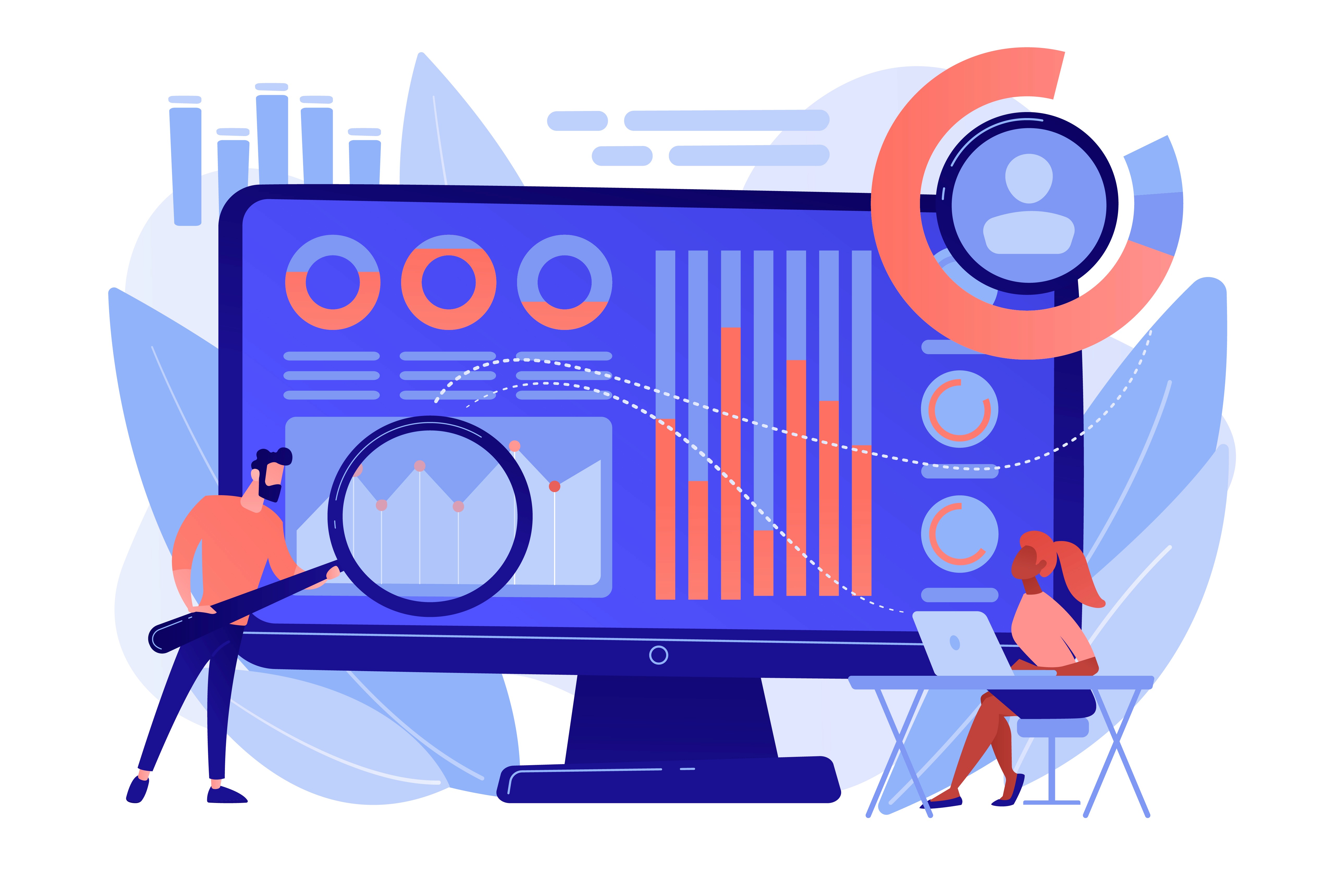
Contexto
En un entorno de fabricación a gran escala, es crucial garantizar una calidad constante e identificar a tiempo las desviaciones del proceso. Los métodos tradicionales de control de calidad, basados en enfoques univariantes o multivariantes básicos, suelen ser inadecuados en entornos en los que los datos proceden de múltiples sensores y operaciones de máquinas, cada uno de los cuales genera grandes volúmenes de datos correlacionados y de alta dimensión (que existe gran cantidad de variables registradas). El control estadístico de procesos (SPC) convencional puede tener dificultades con problemas como la autocorrelación entre sensores o la falta de valores en la introducción de datos en tiempo real, lo que reduce la eficacia de la supervisión y retrasa la detección de fallos que pueden resultar críticos sobre la calidad del producto.
Problema
Supongamos que un fabricante de productos químicos ha estado experimentando problemas de calidad intermitentes con una línea de productos específica. A pesar de aplicar técnicas tradicionales de gráficos de control SPC, la empresa se encuentra con que la variabilidad en determinados parámetros del producto a menudo se detecta demasiado tarde, lo que provoca un aumento de los costes de reprocesamiento y posibles interrupciones en la producción. Además, dadas las interdependencias entre diversas variables del proceso (por ejemplo, la temperatura, la presión y la velocidad de la línea de producción), los gráficos de control SPC tradicionales tienen dificultades para captar los patrones subyacentes y diagnosticar las causas raíz de las situaciones fuera de control.
Solución con LSb-MSPC
Para hacer frente a estos retos, LSb-MSPC se implementa de la siguiente manera:
Recopilación y preprocesamiento de datos:
Se recopilan datos históricos de múltiples sensores (tanto de la máquina como de elementos externos a la misma que pudieran potencialmente influir), centrándose en las variables que se sabe que afectan a la calidad del producto (por ejemplo, la temperatura, la presión del pistón, la velocidad de giro del roscador,humedad de la sala). Los valores que faltan se estiman mediante técnicas de imputación de datos compatibles con los modelos de estructuras latentes.
Construcción del modelo LSb-MSPC:
Mediante PCA y PLS, los datos de los sensores de alta dimensión se proyectan en un espacio latente de menor dimensión, donde se extraen los patrones esenciales del proceso. Esto es como si se realizara un resumen de un texto complejo extrayendo los puntos clave sin tener que leer todo el texto. Gracias a estás técnicas se pueden extraer los patrones existentes en los datos de una forma eficiente.
Se calculan los estadísticos T2 y SPE de Hotelling, que capturan tanto las variaciones del proceso basadas en la puntuación como las basadas en los residuos del modelo.
Supervisión en dos fases:
Fase I: El modelo LSb-MSPC se desarrolla con datos históricos, en control, estableciendo la línea base para las condiciones normales del proceso.
Fase II: Los nuevos datos del proceso en tiempo real se comparan con los gráficos de control establecidos. Cualquier señal fuera de control activa los procedimientos de diagnóstico.
Diagnóstico de fallos y análisis de la causa raíz:
Cuando se detecta una señal de fuera de control, los gráficos de contribución ayudan a precisar qué variables originales contribuyen más a las desviaciones. Esto permite identificar rápidamente variables específicas del proceso -como un aumento inesperado de la presión del pistón o picos de temperatura- que pueden haber provocado los problemas de calidad observados.
Aplicación
En un contexto de fabricación, LSb-MSPC proporciona una solución eficaz para gestionar datos de alta dimensión (muchas variables) y diagnosticar problemas de calidad en procesos complejos. Mediante la implantación de LSb-MSPC:
Control de calidad proactivo: El fabricante puede detectar las desviaciones de calidad mucho antes que con el SPC tradicional, lo que reduce los costes de reprocesamiento y mejora la coherencia.
Gestión de la complejidad de los datos: LSb-MSPC gestiona las dependencias entre variables y los datos que faltan, lo que permite una supervisión más precisa en tiempo real.
Rápida resolución de problemas: Los gráficos de contribución identifican rápidamente qué variables del proceso están causando fallos, lo que permite la resolución de problemas específicos y la reducción del tiempo de inactividad.
Resultado
Con LSb-MSPC, el fabricante consiguió reducir en un 22% los costes de reprocesamiento y disminuyó considerablemente las interrupciones de la producción. Además, la detección temprana de fallos proporcionada por el modelo de estructura latente permitió a los operarios tomar medidas correctivas con mayor eficacia, minimizando las interrupciones, incrementando el entendimiento del proceso y mejorando la estabilidad general del proceso.
Ferrer, A. (2014). Latent structures-based multivariate statistical process control: A paradigm shift. Quality Engineering, 26(1), 72-91.